How to Combat Inflation and Uncertainty Using Digital Tools
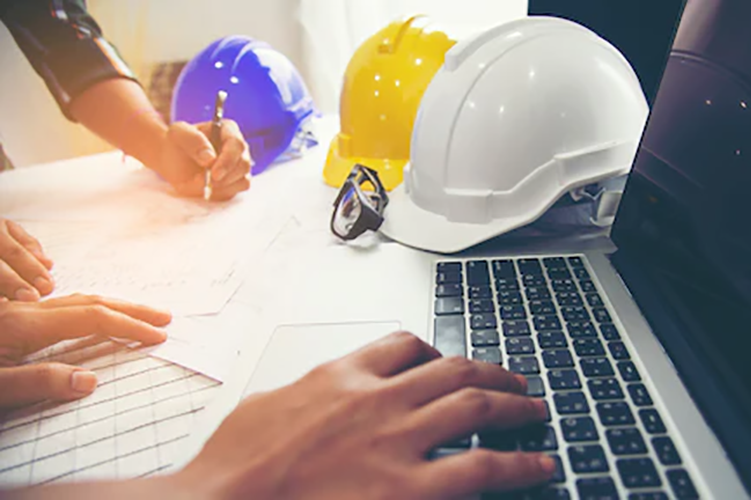
The cost of everyday essentials, including
food, fuel, office supplies, and rent, has skyrocketed due to inflation. This,
coupled with broken links in the supply chain and volatile construction
material pricing, has added significant pressure to the construction industry.
The industry must find ways to overcome these financial hurdles to succeed in
the year ahead.
The Federal Reserve has raised interest
rates to combat inflation, which is forcing significant budget cuts and halting
projects. Construction material prices have risen 16% from a year ago and 41%
since the start of the pandemic, with steel costs soaring over 200% at one
point. Fuel prices have also steadily escalated, with diesel costs rising 33%
in only five weeks in 2022.
Inflation creates complications in cash
flow and project timelines, making it particularly difficult for contractors
and subcontractors who must procure materials in advance and pay for them
before being paid for the job. The $1.2 trillion infrastructure act has
exacerbated challenges by increasing demand for scarce materials.
Asphalt is a crucial component of building
livable communities, and demand for this critical material will continue to
rise due to major projects funded by the infrastructure act. General
contractors and subcontractors must leverage innovative preconstruction
technology to find and win these projects and improve planning, increase
efficiency, and collaborate more easily.
Nearly 40% of specialty contractors still
primarily use outdated methods, such as spreadsheets and paper-based processes.
However, prioritizing innovative construction planning and management
technology can help contractors and subcontractors save money, maximize
efficiencies, and mitigate the adverse effects of inflation. By doing so, they
can improve critical business functions, strengthen collaboration, and be
better prepared for the challenges of 2023.
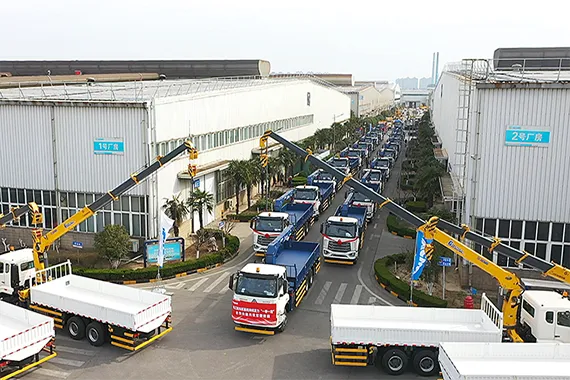
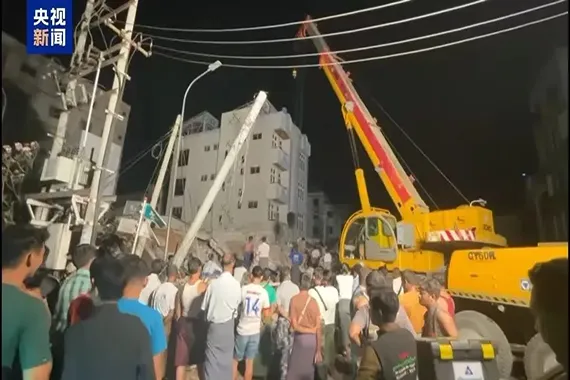
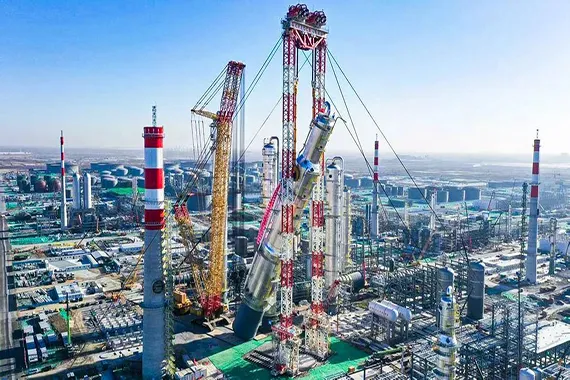
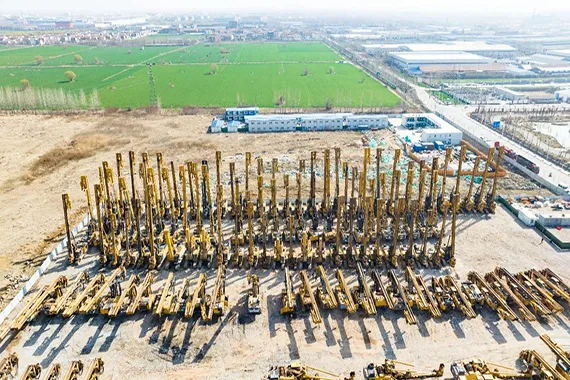
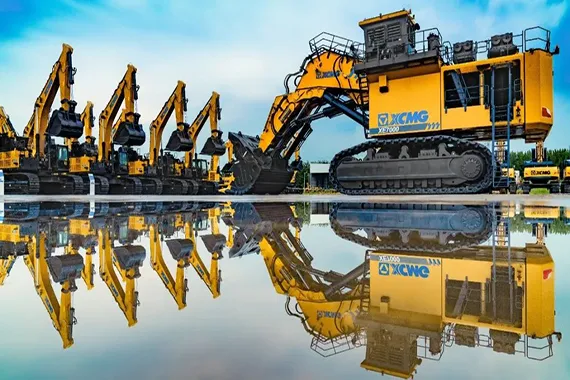