Stacked
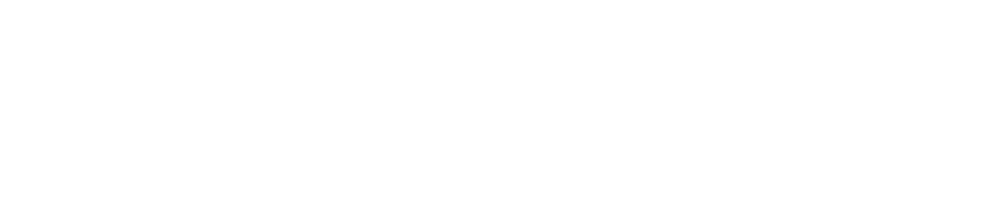
South East Asia is still where you find the
most widespread application of the PPVC (prefabricated pre-finished volumetric construction)
method but it is spreading to other parts of the world. Most projects are
residential apartment buildings and hotels but the method lends itself to other
applications. Fundamental to the lifting work is usually high-capacity top
slewing tower cranes, typically flat tops of 50 tonnes capacity, or more, and
with relatively short booms of 35 or 40 meters.
CRAWLER ALTERNATIVE
A different lifting solution was chosen for
this government PPVC project in Tampines, Singapore. It was a 400 tonne
capacity lattice boom crawler crane. Singapore[1]headquartered lifting and
specialized transport service provider Tiong Woon supplied the XGC400-I made by
XCMG from China. It handled all the precast concrete elements to complete the
hoisting and installation of the multitude of modules, each weighing up to 40
tonnes, making up the apartment building for the Housing Development Board
(HDB). Modular construction and PPVC in particular is becoming increasingly popular,
largely because such precast buildings are economical, safe, long lasting and
quick to build. Instead of employing the usual heavy lift flat top tower crane
for PPVC construction, a different lifting solution was chosen for this project
in Singapore.
ALEX DAHM reports of this type will be
built in this way. Expect to see a large number of low cost economic apartments
built from precast concrete modules in major cities. The XGC400-I has an
infinitely variable superlift function for luffing which is especially useful
in this and many other applications, the manufacturer says. The superlift mast
is 30 metres long, including a bottom section, a 6 metre section, one at 12 metres
and a top section. It has an automatically controlled hydraulic backstop.
Maximum superlift counterweight is 230 tonnes.
A typical single lift for the crawler crane
on this project in Singapore was to hoist, position and precisely place an
entire pre-built room in one operation. It was configured with a standard main
boom and jib combination of 54 + 54 metres. At that the capacity was 60 tonnes
and the longest radius available was 70 metres.
BUILT IN THREE MONTHS
The most obvious benefit of using a crawler
crane is saving construction time, explains Jingling Yang, product manager at
XCMG. Assembly speed for the crane is one of the essential requirements for HDB
since the construction time for the building is only three months, says Yang.“The XGC400-I was assembled in only two days, which was ahead of
schedule. It greatly reduced the time cost. Our crawler crane impressed our
customer, Manikumar, with its high efficiency,” Yang says. Power for the
XGC400-I is from a 338 kW straight six Weichai WP12 turbo diesel. Hydraulics
are Rexroth and it has a Wika LM.
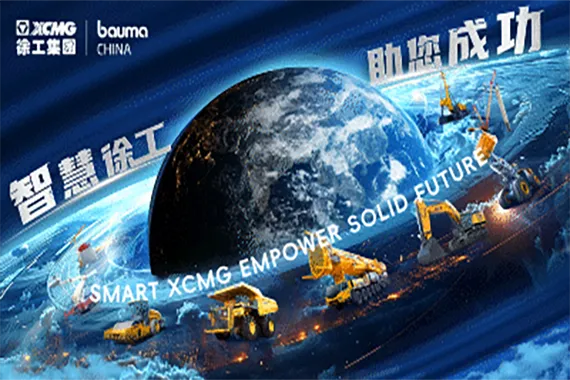
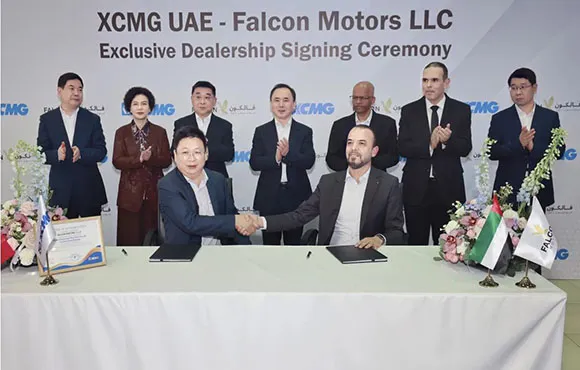
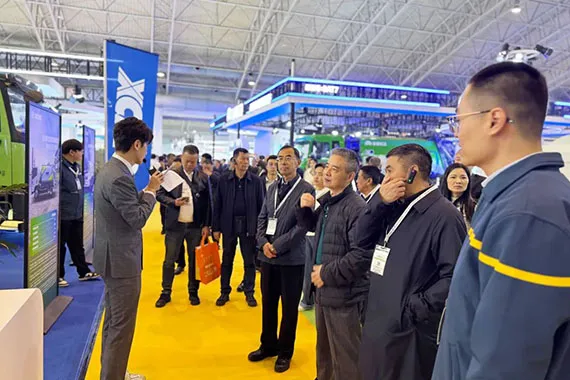
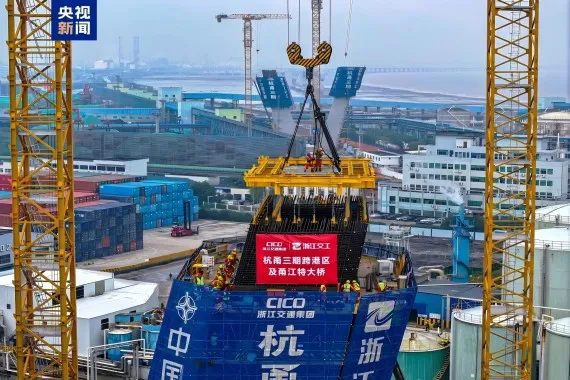
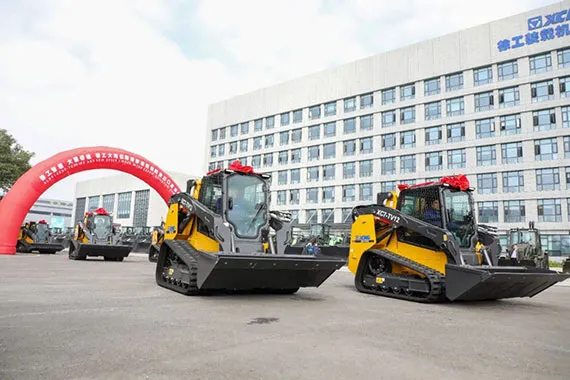