Drum vs. Batch Plant: Learn the Differences That Will Make Your Asphalt Mix Just Right
Often, preparing an asphalt mixture is compared
to baking a cake. A contractor needs to make sure he/she has an accurate recipe
and proper ingredients and that he/she blends everything at the correct ratios
and “bakes” the mixture to produce a beautiful, homogeneous final product that
everyone will be happy with – a blend that will perform as anticipated when
properly applied on a roadway.
There are two basic types of plants that
are used in the process of making asphalt mixtures: batch plants and drum
plants.
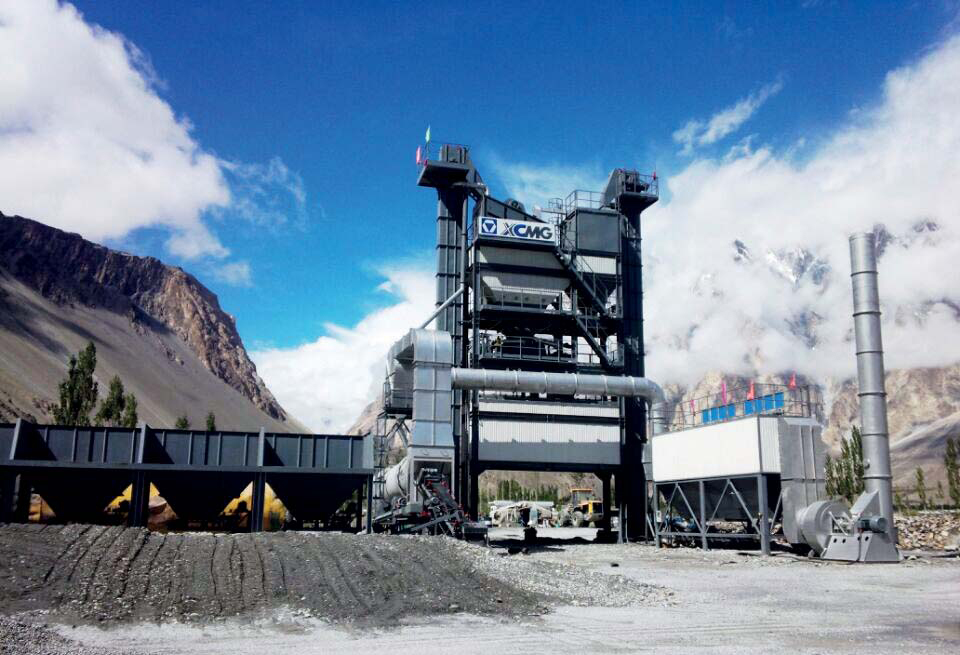
Batch plants make small accurate “batches”
of asphalt mixture through a process that is repeated over and over until the
total tonnage for a project has been manufactured.
The advantages
- They offer the highest level of flexibility in production.
- They manufacture a very high-quality finished
product due to the accurate measurement of each batch produced.
- Batch size and production capacity can vary based on
the designs of the plants themselves.
- Due to the intermittent production process, plant
operators can easily switch back and forth between different mix recipes
if necessary.
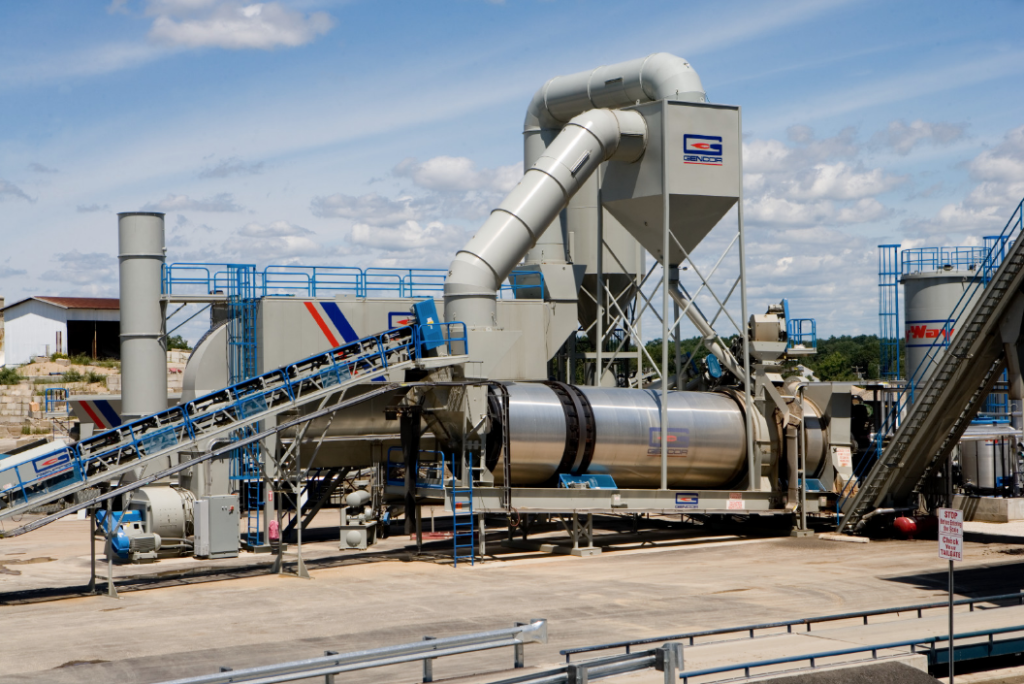
Drum plants, on the other hand, prepare the
asphalt mix through a continuous process and require the use of silos for
temporary storage prior to the mix being trucked to the paving location.
The advantages
- There is no interruption in the production process
as there is a continuous flow of aggregate and liquid asphalt into the
drying/mixing chamber.
- There are several different configurations of drum
plants, all depending on how the aggregate flows in relation to the hot
air, which is responsible for heating and drying the materials.
- In parallel flow, the aggregate and air flow in the
same direction through the chamber.
- In counter-flow plants, the aggregate and air flow
in opposite directions through the chamber.
- In double drum or double barrel plants, there is an
outer shell through which the aggregate flows before coming in contact
with the hot air inside the chamber.
- Regardless of the configuration, it is a continuous
process that creates a homogeneous mixture that can be manufactured at a
high rate (sometimes as high as 600-800 tons per hour).
Main differences:
- In drum plants, there is no interruption
in the production process as there is a continuous flow of aggregate and
liquid asphalt into the drying/mixing chamber. There are several different
configurations of drum plants, all depending on how the aggregate flows in
relation to the hot air, which is responsible for heating and drying the
materials. In parallel flow, the aggregate and air flow in the same
direction through the chamber. In counter-flow plants, the aggregate and
air flow in opposite directions through the chamber. In double drum or
Double Barrel plants, there is an outer shell through which the aggregate
flows before coming in contact with the hot air inside the chamber.
Regardless of the configuration, it is a continuous process which creates
a homogeneous mixture that can be manufactured at a high rate (sometimes
as high as 600-800 tons per hour).
- The ways that aggregate and bitumen (liquid asphalt)
are metered into the final mix are different in batch plants and drum
plants. In batch plants, the aggregate and asphalt binder are
weighted using load cells for accuracy. The aggregate is dried first and
then weighted into the pugmill based on the agency-approved
Job Mix Formulation (JMF). In drum plants, flow meters and calibrated feed belts are used to
measure the liquid and aggregate components into the mixing chamber.
Because the drying and mixing are done in conjunction in the drum plant,
the need to regularly monitor the moisture content of the aggregate
stockpiles is vital to producing a high-quality finished product.
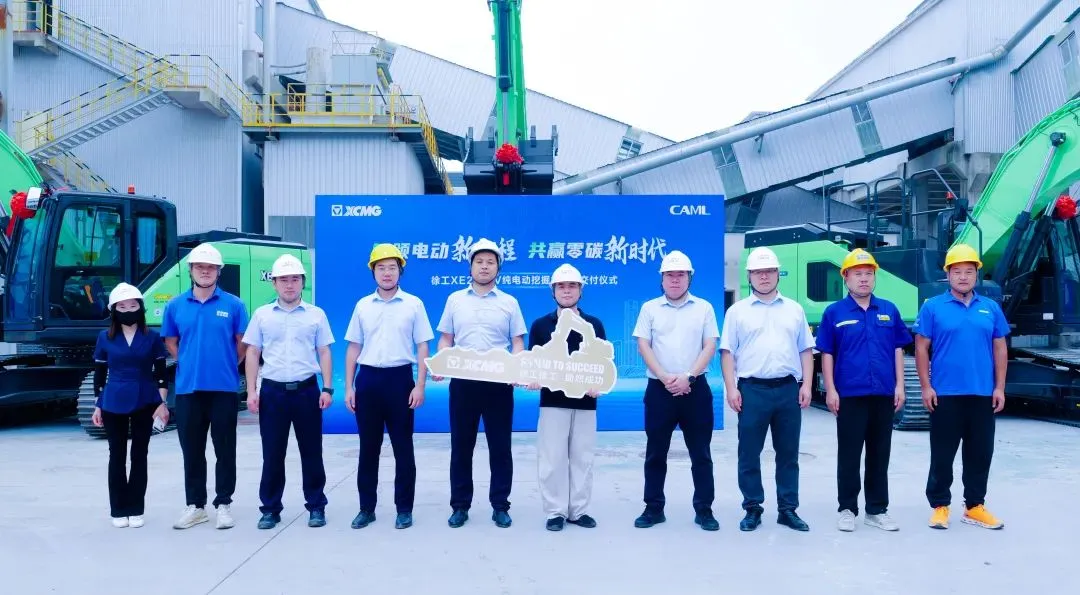
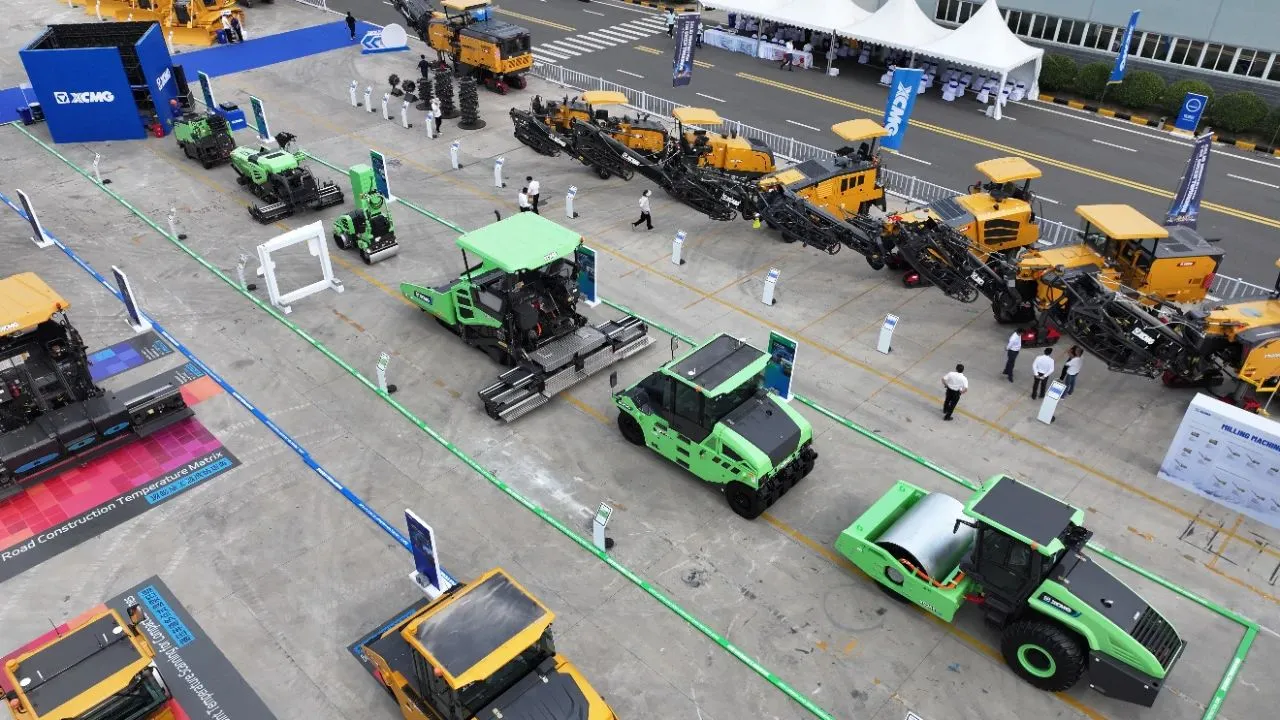
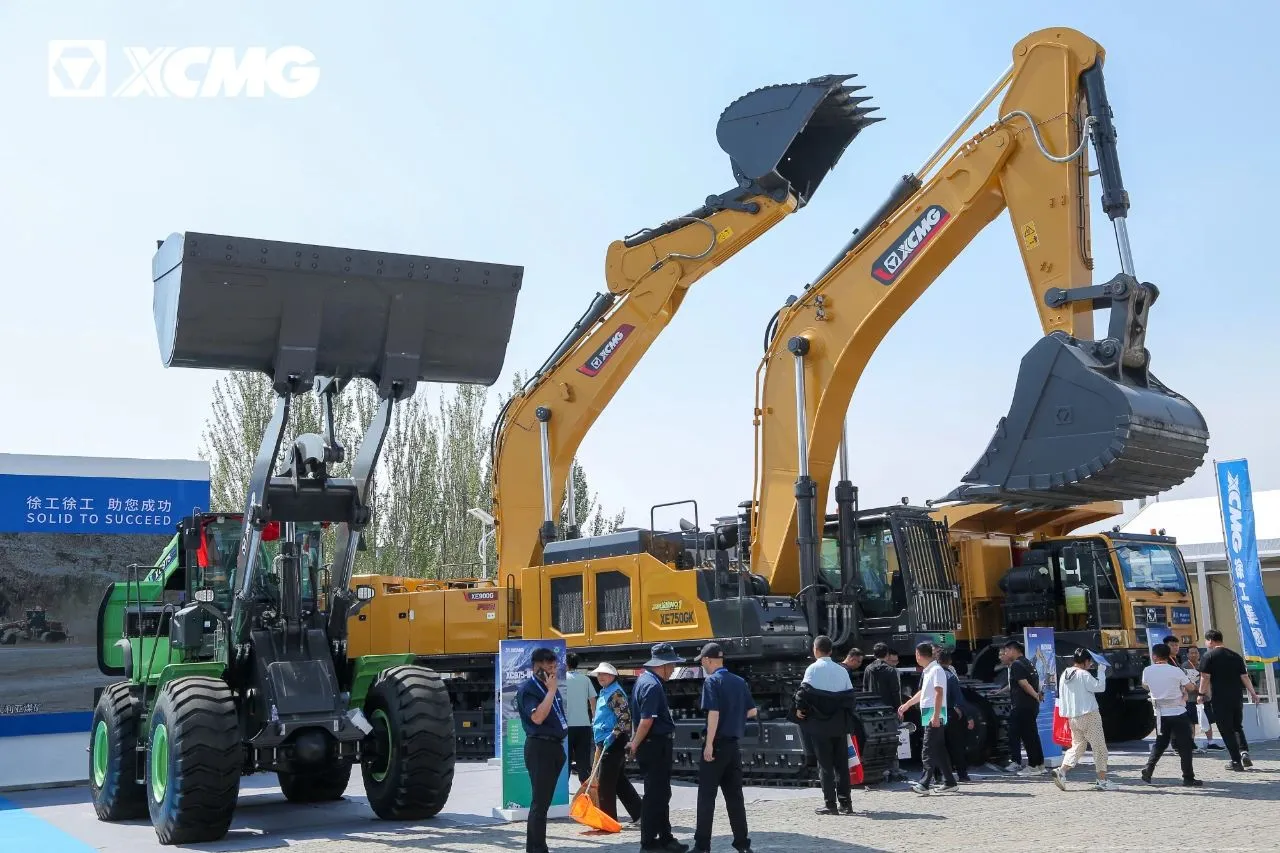
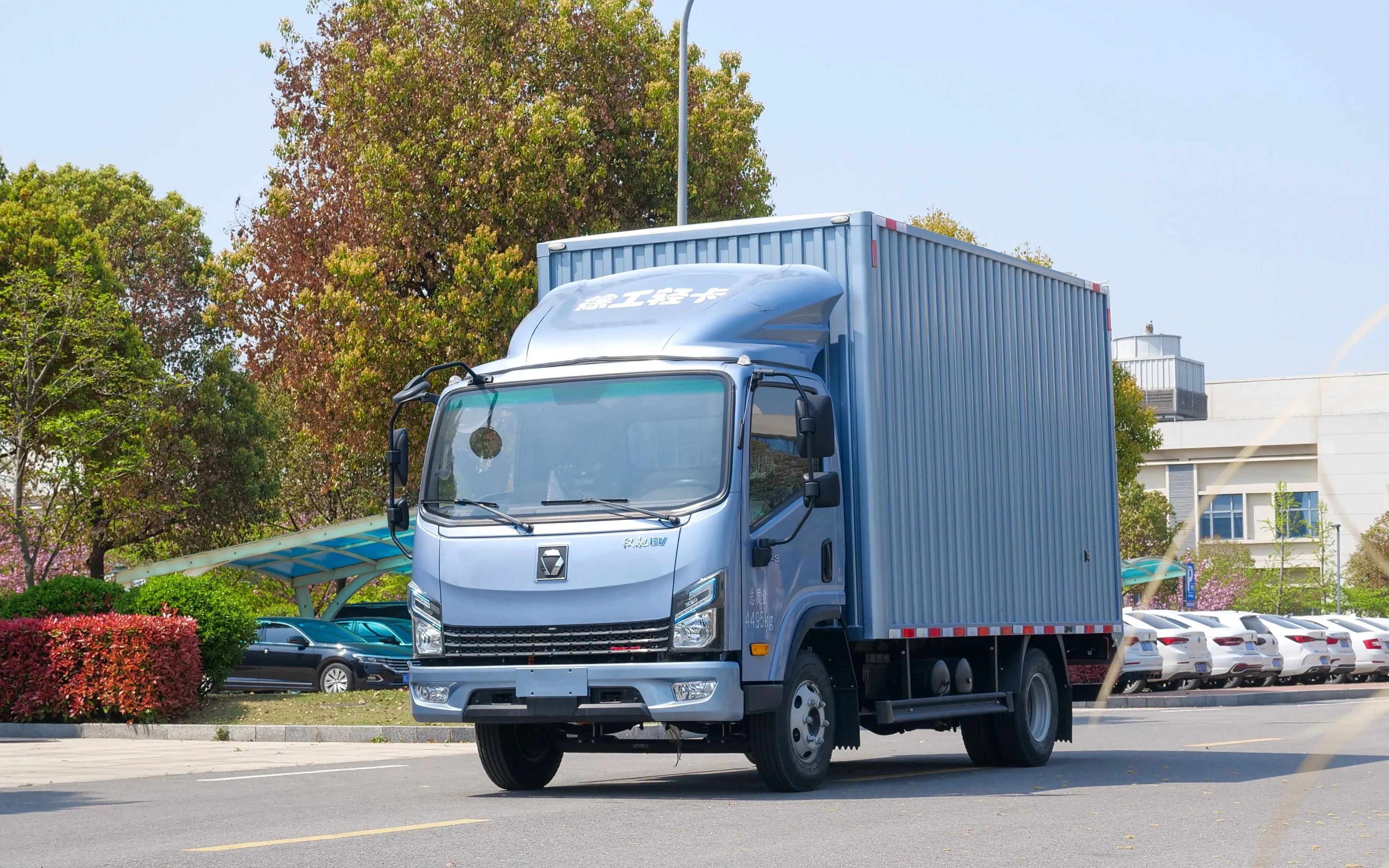
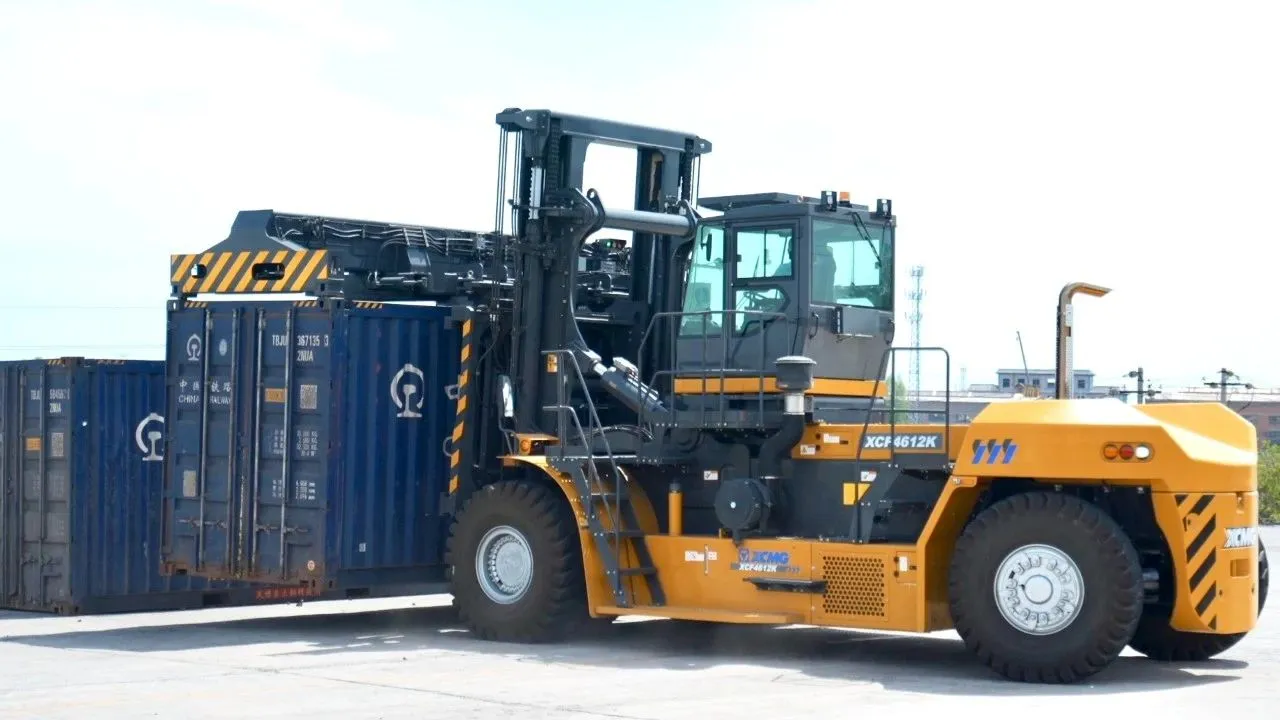